We can probably all think about being more efficient ourselves. What do you want to save? The answer that’s likely to come to mind first is saving time. According to the adage, ‘time means money’ – so perhaps it could ultimately come down to money. But what exactly is involved in becoming more efficient and what does efficiency really mean?
Let’s start with what it’s not. Efficiency is not the same as effectiveness – that’s about getting things right in the first place, and, typically, getting the it right for the customer. We can be effective (get the right result) but still be wasteful and inefficient. So perhaps we should also think about cost-effectiveness– and that is about being efficient as well as getting the right result.
So if efficiency is about not being wasteful, let’s look to the 7 Wastes to remind us of the inefficiencies – and ultimately the opportunities – for savings. There are 8 Wastes if we also include not using all talents and skills to their full potential. TIM WOOD is a mnemonic we use to remember them – let’s have a look…
- T for Transport – when we needlessly move things that we’re processing from one location to another
- I for Inventory – where we hold too much stock, or we create unnecessary work in progress
- M for Motion – if we have a poor office, factory or system layout that requires us to move to collect something which should otherwise be within easy reach
- W for Waiting – we already spoke about time; waiting is potentially wasted time during which we could be doing something more useful or delivering value to our customer earlier
- O for Overproduction – producing more than we need, e.g. food going to waste
- O for Over-processing – if we ‘guild the lily’ we end up with features or capabilities that the customer doesn’t really need, or at least didn’t ask for or want to pay for.
- D for Defects – if we don’t get it right the first time we have to rework or redo it until we do get it right – that indeed costs us money.
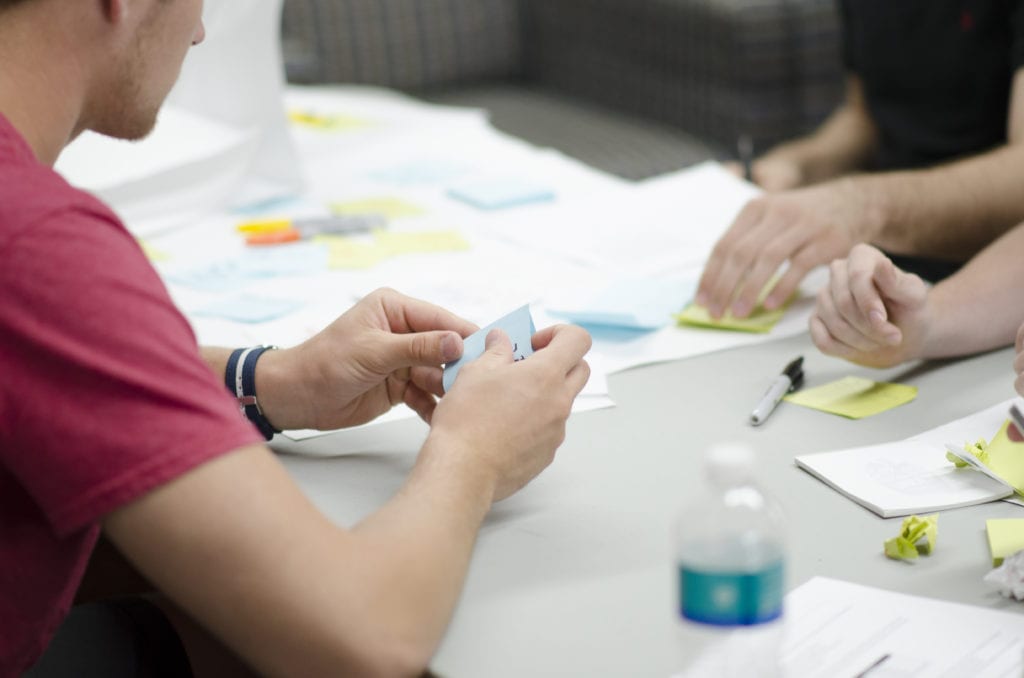
What does this list of waste tell us about efficiency? Certainly, it’s about the efficiency of a process; it’s also about the efficiency of people whether individually or collectively. So, we could have an inefficient sales process, an inefficient finance department, or an inefficient government. Better though to develop efficient ones by identifying the opportunities and addressing the wastes!
Bottom line – it probably is ultimately about money. But it’s also about time, people and processes – and about how we use the resources and assets we have. Money is how we measure its effect eventually.
Come and talk to us at Catalyst about Lean by clicking here. We can help you make your organisation more efficient!